Computer Vision Introduction
The context
Building materials companies play a crucial role in infrastructure development around the world. However, as the demand for these materials grows, so do the challenges associated with the efficient and safe management of their operations, including the processes involved in storage, loading and dispatch. Any delay in product delivery can create construction risks, additional costs, customer/carrier dissatisfaction, as well as negatively impacting a company's reputation.
These factors bring about the need to optimize loading infrastructure and processes to reduce the total loading time, minimize waiting times and guarantee end customer satisfaction. This was the challenge for the multinational construction materials company Cemex, which faced the need to implement a technological solution to improve efficiency in total truck service time, truck management and delivery coordination.
The Mexican company, a manufacturer and distributor of construction materials (such as cement, concrete and aggregates), worked with NEORIS to achieve efficient management, meet market demands, satisfy customers and keep its operations profitable.
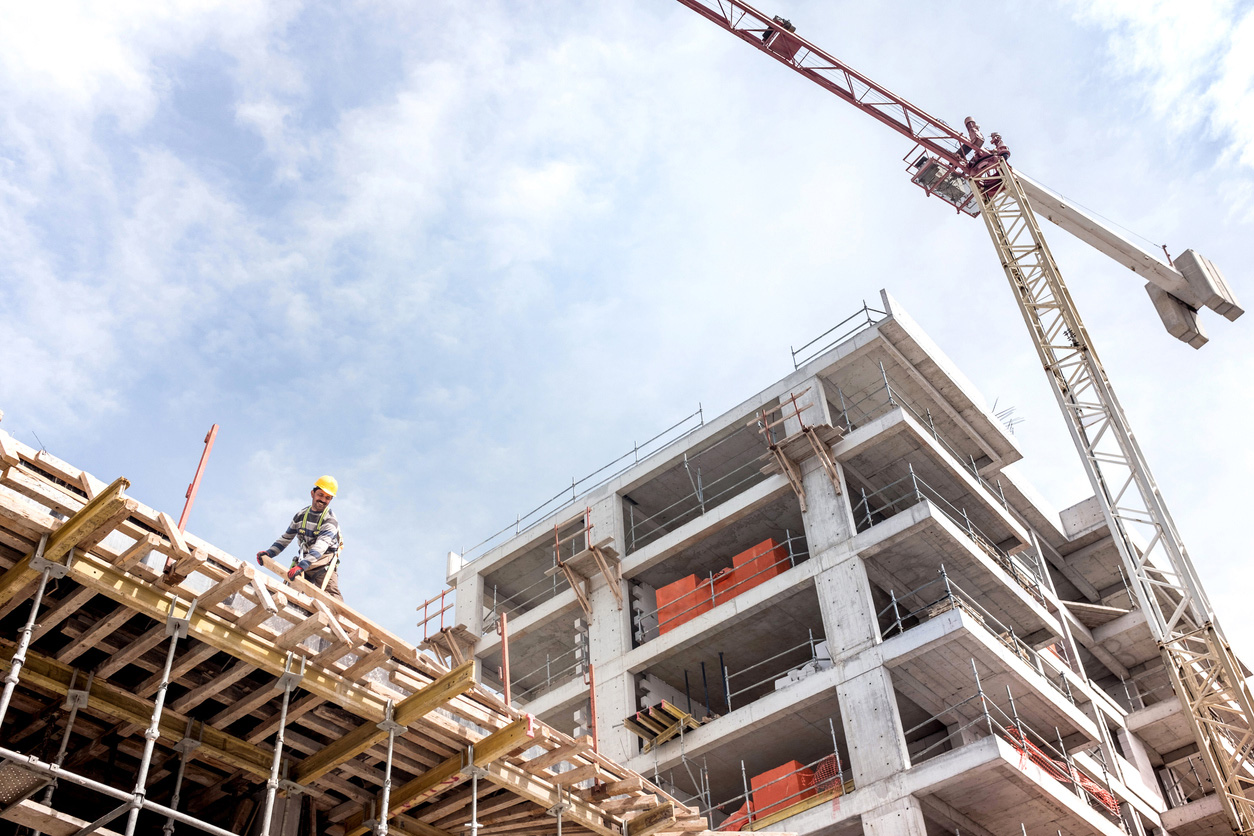
The challenge
Transporting large volumes of construction materials from the plant or terminals to customers can be a complex task. For Cemex, the optimization of this process was essential to minimize costs and service times, calculated as the total time the truck takes from entering the plant empty, loading the product and leaving to deliver the product. Other problems and challenges that the company faced were:
- The solution they were working with had low percentages of recognition levels through image identification and the business opportunities were very limited.
- Lack of visibility in service times. Previously, these were estimated based on anecdotal observation, not on certainties or documented evidence.
- They did not have a history of average loading times to establish a baseline for each plant.
- They could not offer accurate delivery times to customers, running the risk of affecting projects.
- Long truck waiting lines inside and outside the plants, which could cause lost sales.
- Complaints from customers and transport providers due to long service times. A significant number of truck drivers preferred to work with the competition.
- Delays in the plants could lead to economic penalties that could reach up to $200,000 USD per year. When a client filed these late charges, Cemex did not have sufficient evidence to defend itself.
Our proposal
Based on the positive track record of prior successful projects between NEORIS and Cemex, the companies decided to work together to create a totally new solution that was equivalent in functionality, at a more attractive cost and with greater growth flexibility than the solution they were working with up to that time period.
The NEORIS proposal consisted of a solution that would allow Cemex to, among other aspects:
- Use the most advanced technology.
- Accurately measure service times, both total and between intermediate steps and thus establish base times at each plant.
- Identify bottlenecks, to determine areas of opportunity and possible improvement actions.
- Automate the measurement of service times.
- Provide photographic evidence of each loaded truck.
- Instill confidence in the different areas of the business to use this data in decision making and negotiations with clients.
- Use historical information on loading and service times as a basis for future loading estimates.
The implementation of the project ― from proposal stages, analysis and design, to construction, testing and cutover (total migration to the new platform) in the first plant ― lasted about four months and the initially executed version of the solution has been continuously improved and optimized. Over time, the project expanded to other plants and terminals in both the United States and Mexico.
The solution
The solution designed by NEORIS combines powerful object detection and tracking capabilities, accurately identifying behavior patterns within plants, terminals, production facilities and distribution centers. Powered by Artificial Intelligence, the platform enables precise tracking of vehicles and personnel. These capabilities provide the foundation of a customizable solution aimed at improving operational efficiency as well as health and safety for workers.
For technological development, various state-of-the-art technologies were combined, such as image recognition, Edge Computing, neural networks, radio frequency, interfaces, optimizing models and advanced data analytics.
The platform is designed to track vehicles within the facilities to calculate the "cycle time" at each control point: waiting time in the yard, truck loading time, time spent on paperwork administration, departure time, etc.
Gathering this information allows operators to monitor and analyze the process in real time and be alerted to any problems. In addition, the solution helps to:
- Provide historical analytical dashboards to help improve the process.
- Improve the driver's experience inside the plant.
- Know in advance at what times of the day the plant is less crowded to load the truck in less time.
The solution is compatible with devices such as cameras, RFID and QR codes, among others. In the case of cameras, Computer Vision is used to detect the vehicles, classify vehicle type, detect its relevant characteristics and track its movement. Videos can be processed locally in the plant, without the need for a high-speed internet connection or consuming large amounts of bandwidth.
Other features and benefits include:
- Allows for different installation schemes according to the client's needs, with the constant goal of minimizing costs and reducing bandwidth usage.
- Reuse current equipment and infrastructure as much as possible.
- Can be designed to perform centralized processing on the plant floor or in the Cloud, depending on the network infrastructure, strategy or needs of the company.
- It is based on a SaaS (Software as a Service) scheme that allows Cemex to focus on its core business and not on application development.
Challenges and Obstacles
Throughout the project, the NEORIS team faced select challenges:
- Working with cameras in industrial environments in the midst of adverse environmental situations: dust, heat, rain, heavy equipment, darkness at night, etc., all of which affected image quality. We resolved these issues by:
- Training the team with proper safety, maintenance and cleaning protocols.
- Improving detection models, including through the addition of more identification and control elements.
- Installing additional lighting where necessary.
- The increase in the cost of some technical elements of the solution, such as Jetson. We resolved this issue by:
- Changing the architecture by replacing Jetson with a local industrial computer.
The Results
- The solution won the innovation award at Cemex USA in 2022, for the best implementation of innovative technologies.
- The company now has an accurate dataset of its facilities, useful for its Data Science and Analytics teams.
- With the custom dashboard, Cemex obtains operational information with an object location accuracy rate of 90%, exceeding industry standards and without system downtime.
- Currently in process, there are eight (8) plants/terminals in the United States using cameras and one (1) location in Mexico using RFID. Work is in progress on one (1) plant in the Dominican Republic with cameras and another in Mexico.
- Increase in the availability of analytical reports and dashboards.
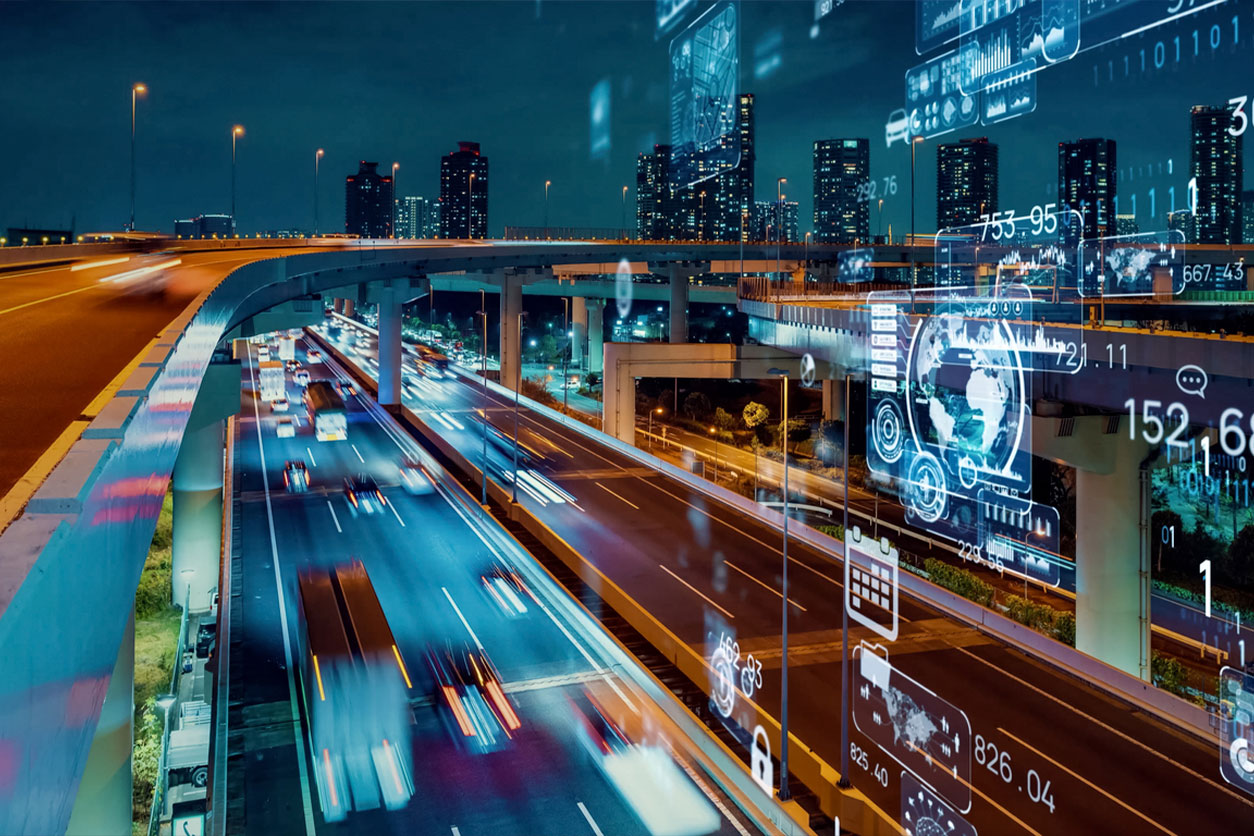
Other Use Cases
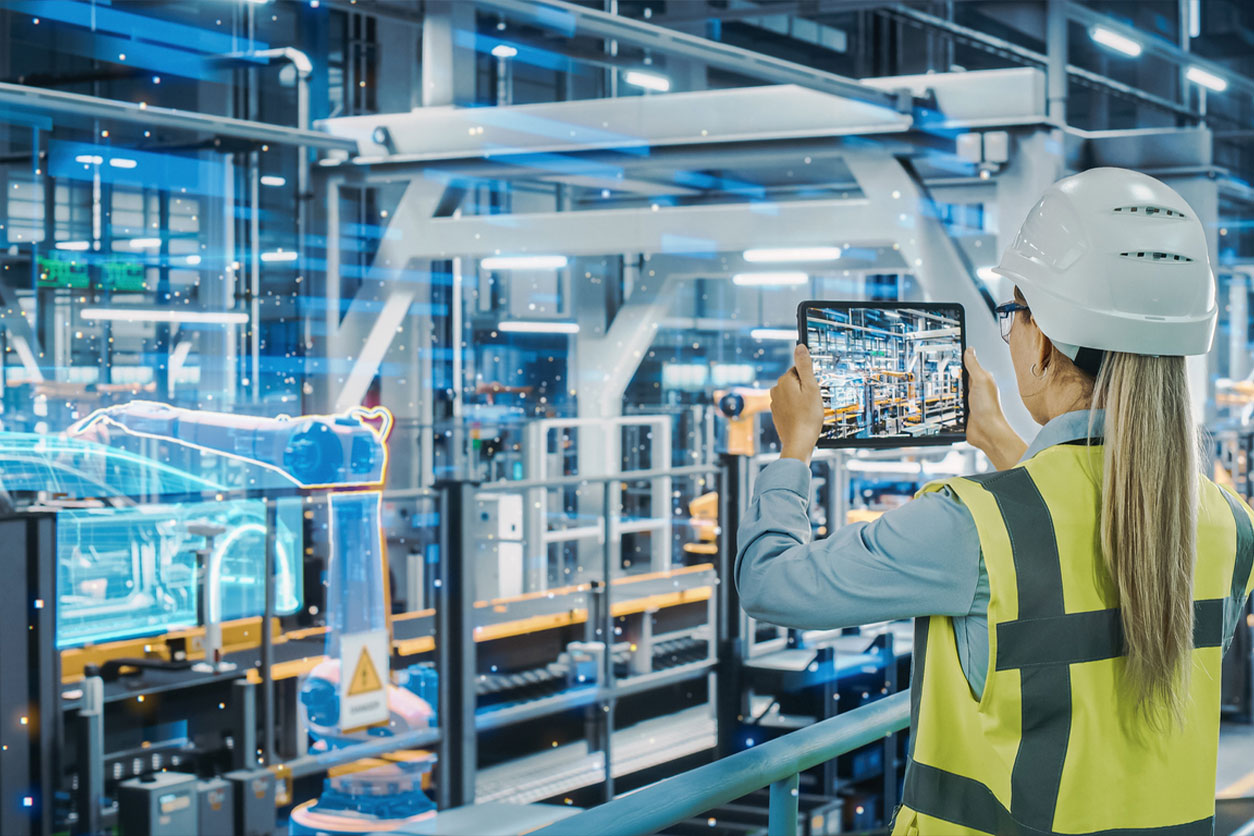
The NEORIS platform has the flexibility to incorporate a wide variety of new custom use cases designed to meet the specific needs of each customer, line of business, and location. Some of the use cases include:
- Health and Safety: Detection of security equipment, people in prohibited areas or near dangerous machinery, physical inventories, validation of the closing of the cement tank hatches, etc. This allows Cemex to integrate this solution with its security initiatives, such as the Zero4Life policy that seeks to eradicate workplace security incidents.
- Train carriages
- Ships and barges
- Physical inventories of trucks and materials (sand, gravel, stones, etc.).
- In addition, detection of damaged product, among other use cases.
Testimonials
“This has been an extremely useful tool for the Miami Dispatch team because it has helped us automate processes, cut delivery times, and above all, reduce errors and maximize employee safety.”
Dagoberto González – Miami Plant“We proactively invested in acquiring and building cutting-edge capabilities in Computer Vision to empower our clients with AI transformative solutions. By harnessing advanced visual recognition technologies, we are able to make a substantial impact through innovative insights, automation, and enhanced decision-making across diverse industries, fostering a competitive edge in an increasingly data-driven world. Our Health & Safety detection models have been a game changer for our top clients, an initiative that is always top in mind with unprecedent value.”
Nir Kaldero – Chief Data Analytics & AI Officer, NEORIS