CdE SAP Manufacturing Solutions
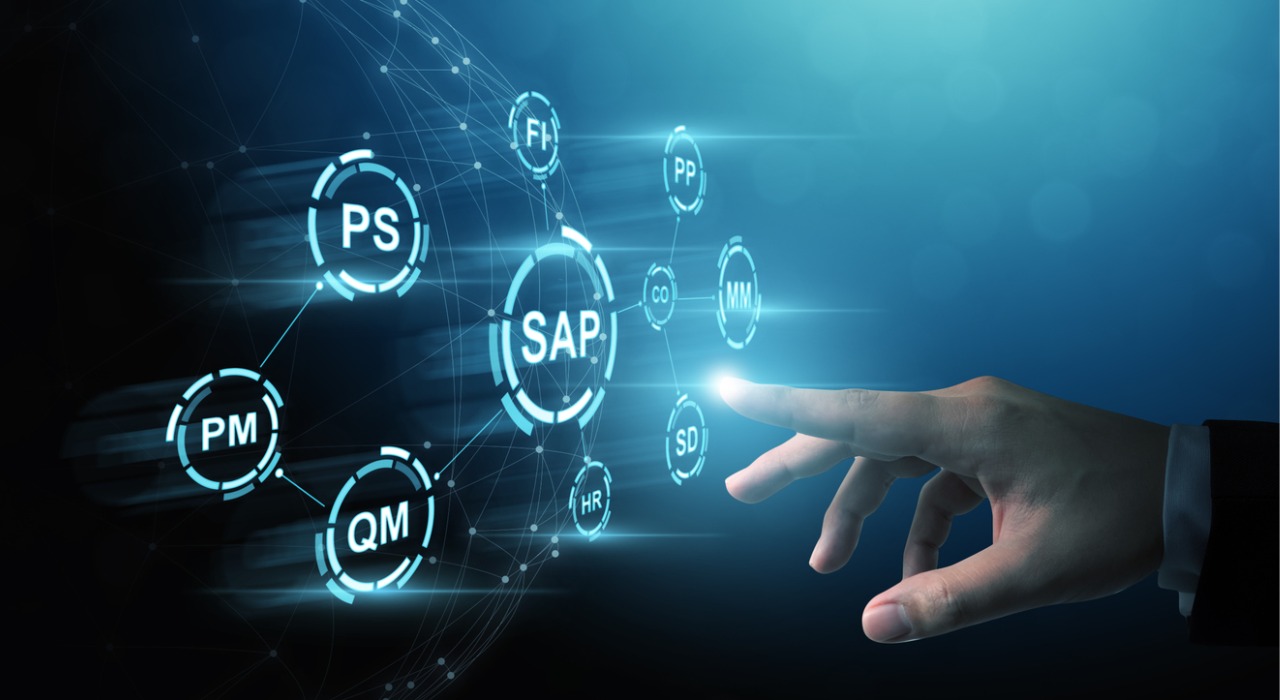
Soluciones de SAP manufactura
para maximizar la eficiencia productiva
The Context
The household appliance industry in Mexico is an important sector within the country's economy with a long history of manufacturing and marketing for both the domestic and foreign markets.
According to data from the Nuevo León Household Appliance Cluster (Clelac), Mexico’s household appliance industry is valued at close to USD 15 billion and the country ranks 5th as a global supplier of household appliances, demonstrating it is a consolidated sector with high growth prospects.
The sector’s high internal demand combined with global trends in technology and responsible energy consumption make it a challenge for companies to stay at the forefront of innovation through the use of technology within this competitive industry.
This was the situation for one Mexican large appliance manufacturer, a leader in Latin America, with 75 years of experience in the market. One of the main manufacturers and marketers of various household products (refrigerators, stoves, washing machines, dryers, microwaves and air conditioners, among others), the Company decided to be firm in its commitment to technological innovation and the quality of its products, undertaking a modernization process to manage different types of operations in its manufacturing sites.
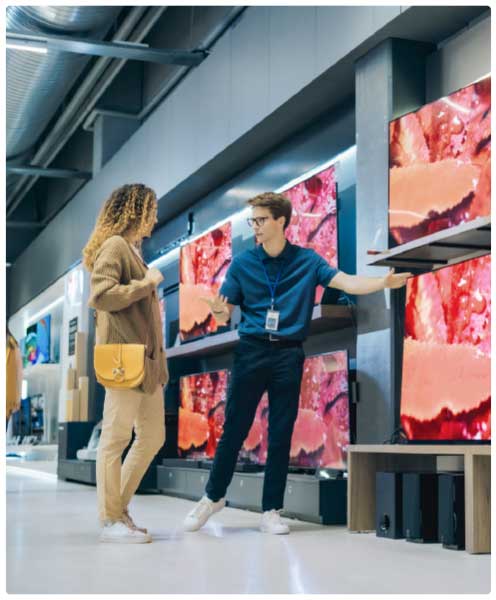
The Challenge
The Company’s specialization of manufacturing sites across a wide range of product lines reflected its versatility and adaptability to market demands. However, this diversity also brought significant operational challenges that impacted the Company's overall management.
Each product line requires a unique operational approach on the production floor to meet rigorous quality and efficiency standards. This need for alignment with the specific requirements of each line creates additional complexity in asset management and productivity across the organization.
This led to a situation where establishing a standardized asset productivity management model across the organization became a priority challenge. The existing model presented significant dispersion and gaps, with inconsistent levels of information detail across operations, hindering decision making.
The main challenges faced by the Company included the need to manage diverse operations, the implementation of specific approaches for each product line, the complexity of asset management, and the inconsistency of information in the current model.
Faced with this scenario, the client chose NEORIS for our proven ability to address complex challenges and design comprehensive solutions that optimize operational management and productivity in complex manufacturing environments, while maintaining high standards of quality and efficiency.
Our Proposal
The proposal presented by NEORIS was characterized by the design of a strategy that covered the entire life cycle of sales orders, from production planning to inventory optimization. To do this, we worked closely with several of the client's business areas and took advantage of SAP advanced technology solutions, such as SAP Integrated Business Planning, SAP S/4HANA Manufacturing for Planning and Scheduling and SAP Manufacturing Execution System (MES/MII), now known as SAP DMC (Digital Manufacturing Cloud).
This collaborative approach for the project allowed the effective and real-time integration of various components of the supply chain, combining on-premise solutions with the Cloud to ensure the flexibility and scalability of the business. Additionally, we committed to providing ongoing support to ensure the long-term success of the proposal’s implementation.
The Solution
The solution developed for the Company covered a series of strategic initiatives designed to improve operational efficiency and performance.
To achieve the goal of covering the entire life cycle of sales orders, from production planning (demand, response to supply, replenishment and inventory optimization) to the scheduling and sequencing of production orders, the automatic creation of purchase orders, transfer orders, deliveries and inventory movements, among other processes, we proposed an end-to-end solution which combined several areas of the client's business and various SAP technological solutions.
One of the key initiatives was the implementation of the Stoppage Response System, which enabled downtime events on production lines to be identified and addressed in an agile manner. This solution leveraged the advanced capabilities of SAP MES (Manufacturing Execution System) and MII (Manufacturing Integration and Intelligence) to monitor and analyze the performance of operations in real time, enabling an immediate response to production problems.
Another notable initiative was the implementation of the Asset Performance Management System, which focused on optimizing the performance of production assets. This solution also relied on the capabilities of SAP MES and MII to collect detailed data on production and asset status, enabling more efficient and proactive management of resources. It also provided valuable statistical information to analyze operational performance and make informed decisions to improve productivity and quality.
Additionally, the integration of SAP S/4HANA - PPDS (Production Planning and Detailed Scheduling) for this customer represented a significant advance in production planning and sequencing. With PPDS, the Company was able to optimize resource allocation and production scheduling to meet market demand more effectively, leading to greater operational efficiency and improved customer service quality.
This solution, integrated directly within the SAP S/4HANA environment, enabled more accurate and efficient production planning.
The Results
The results obtained after the implementation of the proposed solutions translated into significant improvements in the client's efficiency and operational performance along with increased profits. In summary, the positive impact of the project included:
1
Reduced downtime: Early identification and rapid resolution of stoppage events on production lines led to a 25% reduction in these downtimes. This meant greater availability of the production lines and a significant reduction in time losses.
2
Optimization of resource usage: Production became smoother and more efficient, improving the ability to meet delivery deadlines and market demand in a timely manner. This was reflected in a 15% increase in operational efficiency, which means that the Company was able to produce more with the same resources or maintain the same production using fewer resources.
3
Flexibility and stability in planning and programming: The implementation of SAP S/4HANA - PPDS provided greater flexibility and stability in production planning and scheduling. The 20% reduction in preparation times enabled more efficient allocation of resources and more precise scheduling of production activities.
4
Optimization of production capacity: The Company achieved an 18% decrease in manufacturing plant errors through better management of available resources and the implementation of more efficient practices in production processes.
5
Agility in response to demand: The Company improved operational agility by 22%, allowing for faster adjustments in production and a more rapid response to market needs.
6
Overall improvement in the supply chain and increase in profits: Customer satisfaction was increased by 18% by better meeting deadlines and requirements. Similarly, profits increased by 12% and economic and resource losses were reduced by 10%.
These results reflect how each individual area of improvement contributed to strengthening the Company's overall competitive position and profitability in the long term, demonstrating the total positive impact of the solutions implemented.
Testimonials
“The implementation of the solutions proposed by NEORIS has completely transformed our business operations. Thanks to these improvements, we have achieved extraordinary results in terms of efficiency and operational performance. We have managed to not only improve our efficiency and profitability, but also to consolidate our competitive position in the market. We are excited about the future and will continue to take advantage of these improvements to continue growing and innovating in our sector.”
Project Manager on behalf of the client“These improvements have made our day-to-day work at the plant easier and have improved our satisfaction by seeing how our work directly contributes to the positive results of the Company.”
Plant Operator on behalf of the client“The transformation in the client's daily operation has been remarkable. The reduction in downtime and the improvement in operational efficiency are proof of this. The implementation of SAP S/4HANA has brought flexibility and stability to their production planning and scheduling. We are proud to contribute to their path towards operational excellence.”
Orquídea Castillo – Business Account Director at NEORIS