success-case-wheelcompany
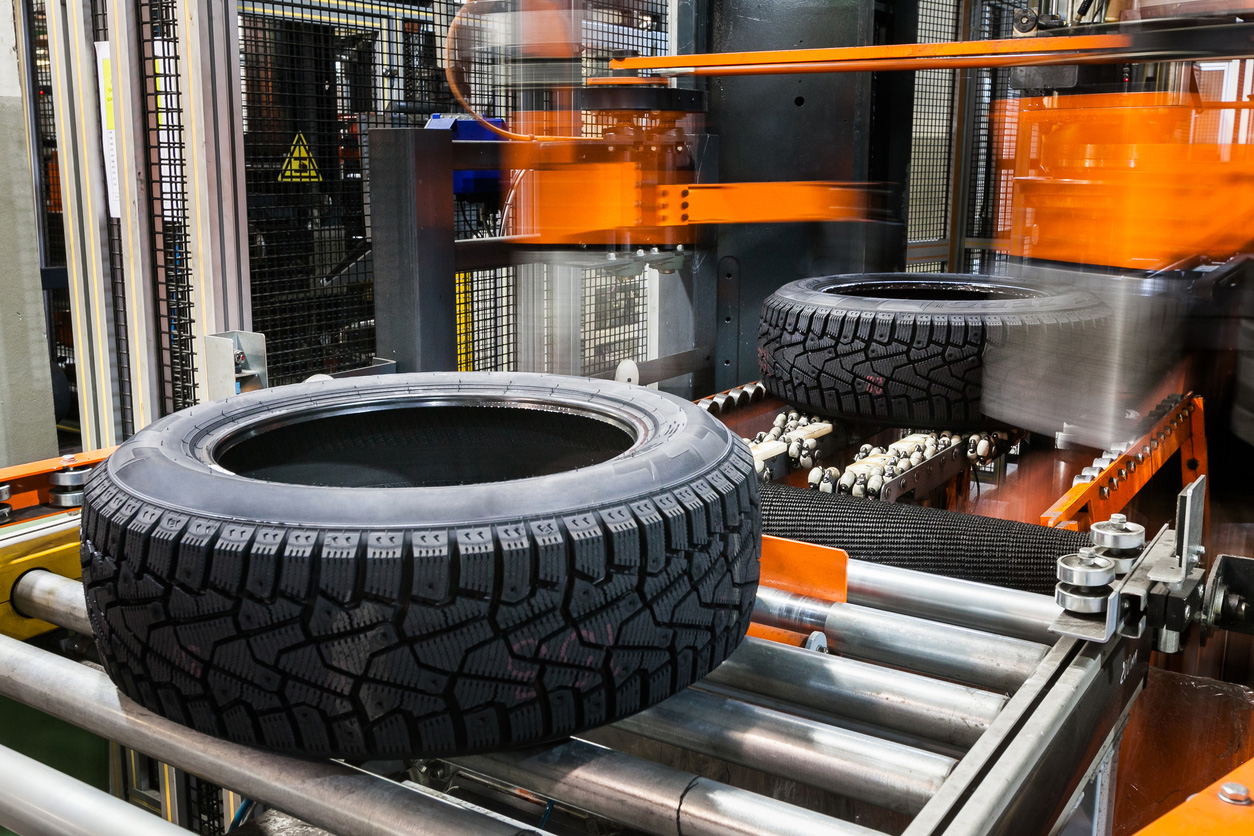
RPA al servicio de la
industria manufacturera
The context
Positioned in the market as a manufacturing industry leader with more than 65 years of experience, the company formed its Continuous Improvement team in 2019 with the aim of designing and implementing the necessary actions to carry out strategic transformational and operational improvements that allow for the automation of several of its processes.
With this challenge in mind, the NEORIS team, together with the company's functional teams, analyzed the existing pain points and detected areas in which there were repetitive processes that not only did not add value, but that also impacted the amount of allocated time and resources.
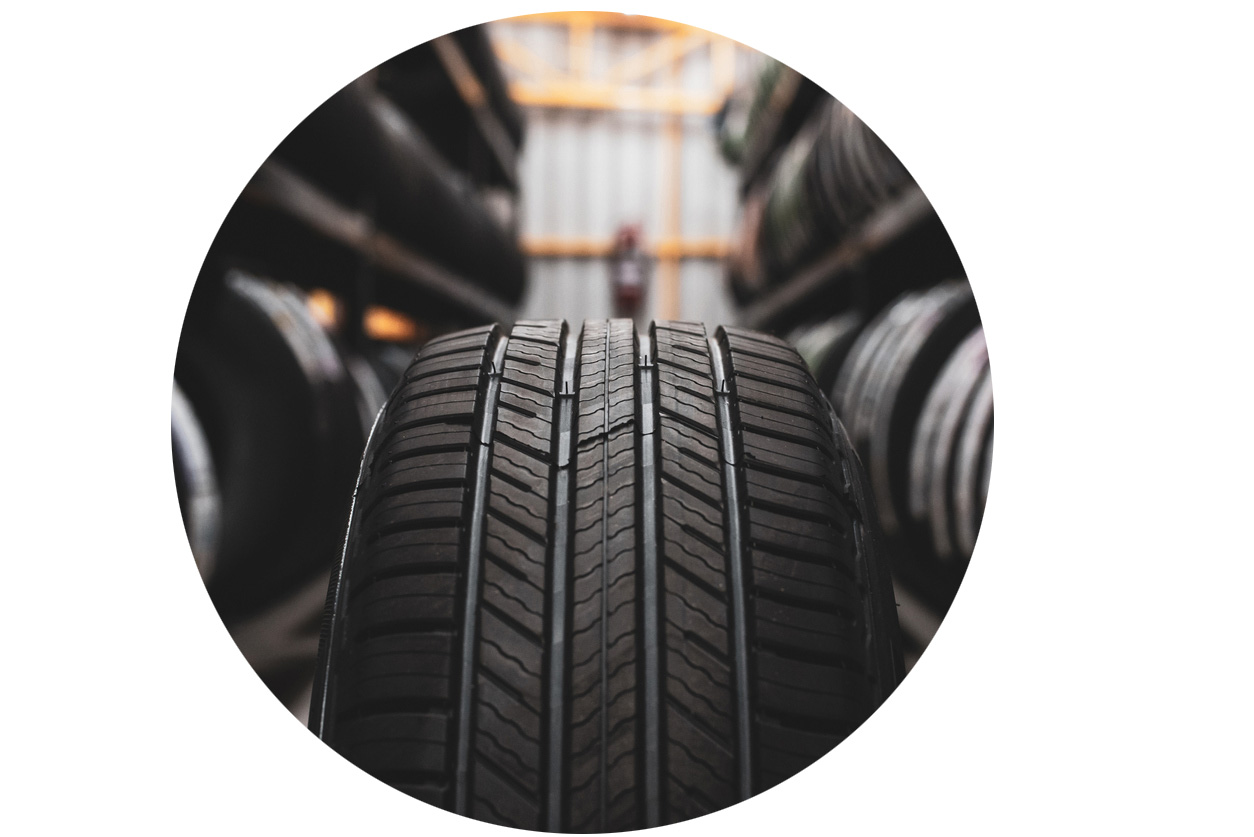
The challenge
It was evident that employees had to perform many time-consuming manual tasks, such as physically printing, manually stamping invoices, scanning and filing documents on a shared drive, or manipulating data in Excel spreadsheets, among others.
The company needed more efficient methods to save time and costs, so the Continuous Improvement team worked with the other involved teams to drive digital transformation through process automation. (RPA).
Our proposal
NEORIS partnered with this industry leading company to implement a new intelligent automation program using Automation Anywhere. The different teams involved in the project defined the architecture of the automation platform, the structure and responsibilities of the team to cover the services through process mapping, development and the maintenance of bots, service level agreements and process documentation, all while establishing expectations of different users. In addition, specific metrics and reports were defined to continue evolving and improving the provision of services in the future.
An essential part of the work with the client's IT team was to establish a monitoring and support system for problem solving, based on the categorization of the severity of each particular bot. Through this, it became possible to prioritize the problems needing priority attention in order to allocate resources appropriately.
Tools used:
- Agile Methodologies (combination of SCRUM and Kanban).
- Automation Anywhere v360, IQ Bot, Jira and GIT.
The solution
After an extensive and in-depth analysis of the variables, as well as the goals established in terms of optimization and productivity improvement, the automation process began in 2020. This heralded a change in the culture and thinking of the teams, who needed to trust what automation could do for them.
The project formally began in May 2020 with 26 professionals involved, including Project Managers, architects, business analysts, and developers.
It began with the automation of five processes, with a first contract for 45 bots. Once this first challenge was overcome during the first year, it was agreed to extend the contract to 45 additional bots, reaching a total of 90 bots.
In May 2022, having exceeded 90 implemented bots, a model contract called "Bot Factory/Automated Steps" was agreed with the client, in which services were expanded and added to those already offered:
- Process mapping and analysis(new).
- Development (existing)
- Support and maintenance (new)
- Platform migration v11 to v360 (new – one shot).
Similarly, the committed productivity that the team would have was also defined, according to its new dimensions for the coming years. This productivity will be measured in the number of process steps to be implemented. For all of this, we agreed to sign a 3-year contract, until June 2025, setting our sights on meeting the following objectives:
- Automate +1320 steps per year, with 3 developers.
- Support to +440 steps per year, with 1 developer.
- Generate activity processes (pipeline) documented for 4 developers, with a business analyst. This would mean approximately 1,800 documented steps per year.
- Support the Automation Anywhere platform for the migration to the new 360 version for all bots, which would take two months.
Taking into account the good production rate that was achieved, the company proposed to expand the number of resources, as well as the production rate, opening the possibility of using new technologies, such as the introduction of cognitive capabilities in automations through the implementation of the IQ Bot module of Automation Anywhere, the analysis of processes through 100% data-driven platforms of Process Mining or the implementation of Conversational Assistants that allow connecting the automations carried out in the back of the organization with the front of the channels of interaction with end customers and employees.
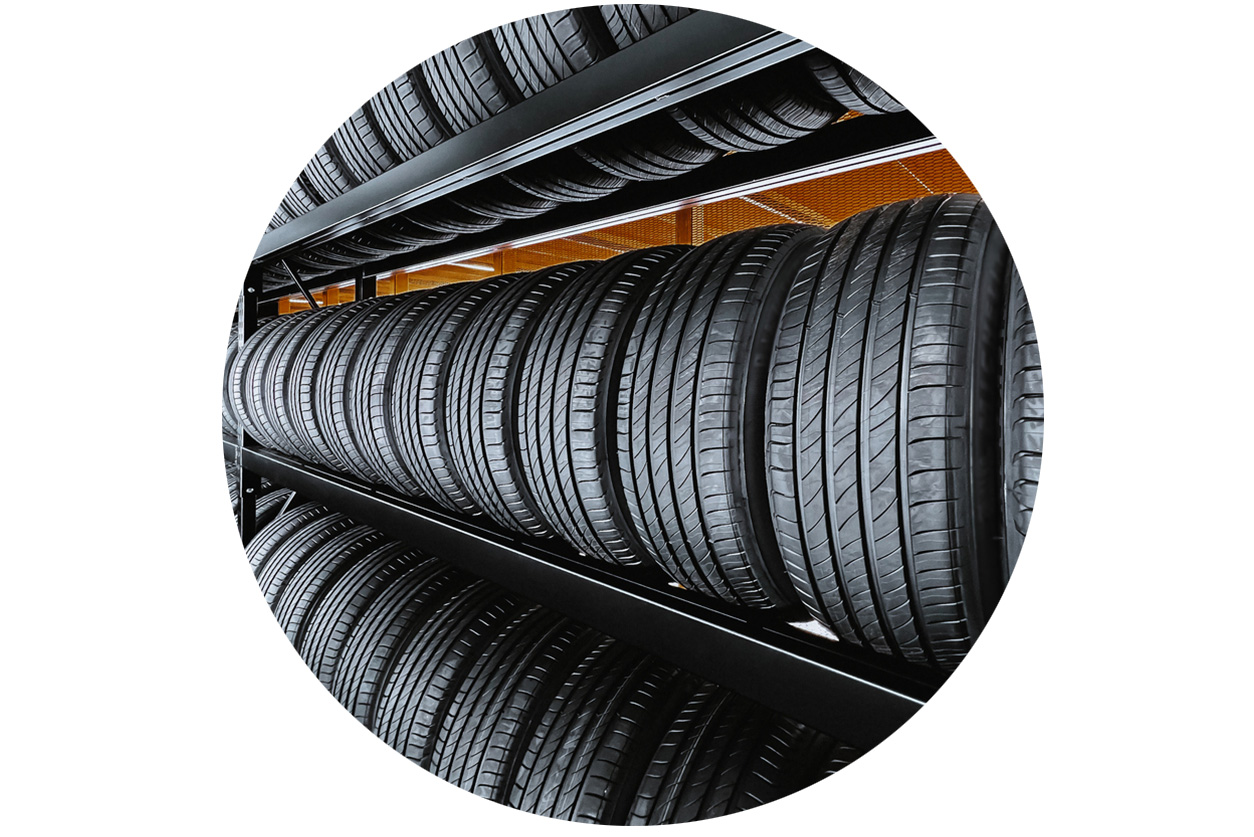
Key points of the project:
- Definition and implementation of "Policies and Procedures.”
- Internal daily follow-up and with the client.
- Definition and preparation of templates.
- Definition of the maintenance and support model, defining the Service-Level Agreements (SLAs).
- Definition and implementation of the general work methodology, ensuring that the entire team is focused on the objectives of the contract.
- Continuous feedback with the team to avoid the slightest impact that may arise due to the possible rotation of resources (testing, validation and running).
How do we face and adapt to the unforeseen?
- Time Difference: We have professionals in India, Spain, Peru, Brazil and Mexico.
- Cultural Difference: We align ourselves with the client's culture to better understand their expectations: punctuality, deadlines, communication, etc.
- Language Difference: We have a skilled team that includes members with a command of English, especially among our business analysts who constantly interact with different business users.
- Pandemic: Managing the project remotely has been a major challenge. Daily monitoring and continuous feedback were essential to motivate staff members and achieve the objectives. Faced with the economic crisis caused by the pandemic, RPA was the solution to save and obtain a relevant ROI.
- Staffing Rotation: Several business users with whom we started the automation projects left the company, so we rethought and redesigned the proposals for the new staff members.
The Results
The success of the initial automations fueled internal adoption, prompting this industry-leading company to rapidly expand its intelligent automation program to more than 70 processes, while continuing to receive ongoing requests. What were we able to achieve?
- 30,000 hours saved annually (USD 1.7 M).
- Automation of +70 processes (+70 processes or +100 robots. A process can have several bots).
As a goal, the company set out to achieve additional savings by Q1 2023 of USD 500,000.
Testimonials
“RPA empowers business users to guide them to perform strategic activities instead of repetitive tasks that consume too much time.”- RPA Director.
“We have had tremendous support from senior management for our automation program.”- Manager of Continuous Improvement Processes.
“Automation through robotics has helped us transform and automate many processes, allowing associates to focus on more value-added tasks.”- Vice President of Continuous Improvement.
“Increasing the efficiency ratio of the company, through hyper-automation, is the result of changing the mindset of the company to place automation at the center of each initiative or task.”- Global Director of Digital Strategy and Operations Transformation at NEORIS.